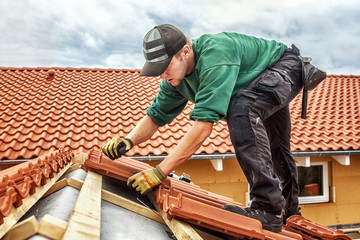
Keep pets indoors: Hammering and vibrations can disturb dogs, cats, hamsters and other animals. Also, they can accidentally step on stray nails or debris.
Protect your plants and yard: Roofers may need to tarp around landscaping features, such as koi ponds tucked behind reeds or hidden waterfalls. Also, consider moving any movable objects and cover them with tarps. Contact Sun City Roofing Pros for professional help.
1. Preparation
The first step in roofing installation is to prepare the sheathing. Roofers check the condition of the sheathing, making sure it’s smooth and tightly fastened to the roof trusses. They also look for any weak spots, moisture, damaged areas or nails that need to be removed or pounded flat so they don’t tear into the new shingles.
Once the sheathing is prepared, roofers lay the underlayment, which consists of self-stick ice and water underlayment and tar paper. This layer seals the vulnerable edges of your roof to keep water and snow out. After the underlayment is in place, the roofers install the shingle strips. They use a nail gun to speed up the process and ensure that all the shingles are properly installed.
During the shingle installation, the roofers stagger each course of shingles so that the joints and breaks are offset from each other. They also use a hook blade to trim off any shingles that extend beyond the roof edge, which gives it a more streamlined appearance. At this point, they’ll also install flashing around chimneys, vents, windows and other vulnerable spots.
The roofing process can cause vibrations and kick up a lot of dust inside your home. To protect your belongings, clear the attic of any valuables or family heirlooms and move them to a safe location in the house. Also, remove any hung decorations that could become loose and damage your walls.
Keeping children and pets away from the work area is important for their safety as well as that of the roofing crew. It’s best to have them stay with friends or family during the project so they aren’t exposed to the noise, vibrations and other distractions of a roof replacement.
2. Underlayment
The roof over our heads isn’t a single material, but multiple layers that combine to form a whole roofing system. While homeowners may be familiar with shingles, tiles or metal, they might not know the crucial role that underlayment plays in the longevity of their roof. Underlayment is a waterproof base that is installed directly on a roof deck before the final roof covering. It acts as a barrier to shield the roof deck from water infiltration and condensation, protecting the residence against adverse weather conditions like heavy rain, wind, hail and UV rays.
Before installing the underlayment, contractors must ensure that the roof deck is in good condition and free of rot or moisture damage. The contractor must also sweep away any debris and dirt that could affect the performance of the underlayment or the shingle installation.
There are a few types of underlayment that a homeowner can choose from, including asphalt felt, synthetic underlayment and self-adhesive underlayment. The type of underlayment a homeowner chooses depends on the needs and budget.
For example, asphalt felt underlayment is a cost-effective choice for roofs that will be covered with shingles. It is also easy to install and works as a smart vapor retarder by changing its permeance depending on whether it’s dry or wet.
Synthetic underlayment is another option that is usually made from a mix of materials, including polymers and plant fibers. It is more resistant to tear and has an asphalt coating that makes it waterproof. It is recommended to use a roofing tape or sealant to seal lap seams when using this underlayment. It is important to note that not all synthetic underlayments are a vapor barrier, so it is best to check the manufacturer’s instructions when choosing a specific product for your home.
3. Shingles
The most visible part of your roof is the shingles. They are usually installed in courses, or rows, beginning with the bottom row and working up the roof to the ridge. Each shingle has its own unique pattern and should be cut correctly for a good fit. This includes proper exposure (the portion of the shingle that’s visible after it is installed), offset (the lateral distance between joints in successive courses sometimes called stagger) and nail placement. The shingle packaging should have instructions for these issues.
Asphalt and felt-paper underlayment must be laid before the shingles are installed. Depending on the kind of underlayment you use, this may be a standard 15-pound felt or a special waterproof material that requires no nailing. Start at the lowest point of the roof and work your way up, overlapping each strip by half its width. Follow the instructions on the underlayment packaging if you have any, which will often include suggestions for staggered rows if your roof is large or if it is an unusual shape.
After the underlayment is in place, it is time to install the first course of shingles. Begin with the shingle farthest from the eaves and work your way up to the ridge. This process is referred to as “stepping” or “racking.” When installing the first shingle of each row, you may want to consider using a full-sized shingle and then cutting it down to size for the rest of that row. This can help make your shingle rows look more uniform and it makes it easier to keep the tools you need next to you without having to move them all the time.
4. Flashing
Roof flashing is a sheet of impermeable material that prevents water penetration or seepage into walls and roofs, and directs rainwater to specific areas where it can be absorbed. It’s installed to surround any roof features, including vents, skylights, chimneys and dormers, and is often made of metal. It also helps seal joints and seams.
The flashing process is a crucial step in the roofing installation, especially for the parts of your roof that connect to other structures. The flashing is typically made of a non-ferrous metal, such as aluminum or zinc. This helps prevent water from entering the attic and damaging your home. Flashing also covers gaps between, for example, masonry and sheathing or wood. Masonry expands and contracts differently than sheathing or wood, so if these materials touch without a barrier, water can leak underneath and damage the structure beneath it.
Some parts of your roof require two pieces of flashing, such as the roof valleys or any points where a roof meets a vertical surface like a wall or dormer. To prevent roof leaks in these areas, the flashing is designed to overlap. The bottom of the flashing is nailed to the sheathing or shingles and the top of the flashing is nailed to a corresponding point on the wall or dormer.
Some types of flashing also have a built-in drip edge, such as the kind found around a dormer or chimney. This protects the flashing from water and snow, which can cause it to rust. In addition, the drip edge is typically made of a different material than your roof’s sheathing or shingles, such as copper, galvanized steel or lead, which adds an extra layer of protection.
5. Ridge Cap
Ridge caps protect the roof ridge line and provide a clean, finished look to the roof. They also help uphold the structural integrity of the roof and prevent water damage, mold, mildew, and shingle wear. Proper ridge cap installation and maintenance helps extend the life of the roof.
When choosing a ridge cap, homeowners can choose between solid closures and vented ridge caps. Both have their own benefits and advantages, so understanding the differences between the two is important for homeowners to choose the best one for their roof.
Installing a ridge cap is an easy process that can be done in just a few steps. Start by measuring the ridge line to determine how many pieces of ridge cap will be needed. Be sure to account for the 6″ overlap and 1″ to prepare cap ends. Next, lay down the first piece of ridge cap and mark it with a carpenter’s pencil along its outside edges. Repeat this step for the other side of the roof. Once the chalk lines are marked, use a screwdriver to pry open the hems of each end and cut away one inch from each. This will help ensure that the end caps fit correctly, properly covering the ridge and ensuring no gap is visible.
Lastly, apply roofing sealant to the ridge cap’s seams and edges. This will ensure that any water leaks or other problems don’t get into the interior of the home. With proper care and maintenance, a well-installed ridge cap can last between 10 to 30 years. Regular inspections are important to identify and address any cracks or other issues quickly, before they become more serious.